
The Chrysalis
Multidisciplinary Collaboration for Parametric Design and Construction

Memorable events in our human experience are often associated with memorable places. Places can shape our experience of emotions and our ability to connect with one another. This is perhaps the most significant role of architecture in society: to shape, uplift and even restore humanity by creating space for memorable experiences. The Chrysalis was conceived to be a one-of-a-kind place that is delightful and unexpected – a project that is transformative to its surroundings as a special place of cultural significance.
The Chrysalis is at once a performance stage, park pavilion and sculpture, serving as a destination within the park as well as a venue for large shows and festivals. The 5,000 sq. ft. high-performance structure is designed to accommodate major programs with two prosceniums for small or large performances. Additionally, it can flexibly host a variety of events as a simple outdoor shelter.
Working in collaboration with parametric designer Marc Fornes, the design team developed the design of the Chrysalis as an organic form that is simultaneously natural yet highly tectonic, presenting a convergence of oppositional readings as both integrated with its forested surroundings and distinct from it. The geometry responds to site conditions such as tree locations, grading and orientation while also forming apertures for viewing and performing. The result is a see-through sculptural object that demands to be experienced in the round, ever changing for the viewer.
To achieve this, the design process entailed a unique level of collaboration, blurring the lines between architecture, structural engineering, and fabrication. The fully integrated design process exclusively utilized digital models for communication and coordination over traditional 2D orthographic projections like plans, sections, and elevations. As such, the Chrysalis required innovative approaches to analysis, design, and detailing, at each turn requiring optimization that challenged standard courses of practice. In this way, the Chrysalis is exceptional not only for its dynamic form and presence, but also for the fully integrated, interdisciplinary design process necessary to bring it to realization.
The Chrysalis is exceptional not only for its dynamic form and presence, but also for the fully integrated, interdisciplinary design process necessary to bring it to realization.
The basic elements of the Chrysalis are the stage, superstructure, shell and shingles. The stage is formed of concrete piers and deck covered with wood decking tiles and a wood railing system. The sections of the rolled steel tube superstructure are each unique in length and curvature, creating an elegant framework of asymmetric arches. The shell itself is made of a proprietary aluminum panel system. These unitized panels are self-spanning, with 300 completely unique integrated aluminum trusses covered with aluminum sheathing. The superstructure and shell were field assembled by crane in a carefully sequenced process of erection. The shell was then covered with 8,200 aluminum shingles in 44 unique profiles applied in a four-color gradient.
While technically advanced, the design works to unify its elements to a cohesive whole that is striking and remarkable. The spatial and formal qualities of the Chrysalis are meant to compliment the cultural programs it houses. Together, the effect is a place where indelible memories are formed for community members, concertgoers and visitors alike.


In an effort to remain faithful to the original vision, the team studied the viability of a rigid shell structure composed of through fastened aluminum plate shingles. Through an exhaustive computational analysis, models demonstrated two key vulnerabilities to the design strategy.
Without loading, the shell integrity could be sustained. However, when loaded with heavy point load factors needed for theatrical equipment suspension, the shell would fail catastrophically. Also, under wind loads, the organic geometry could buckle and deflect beyond tolerable limits.

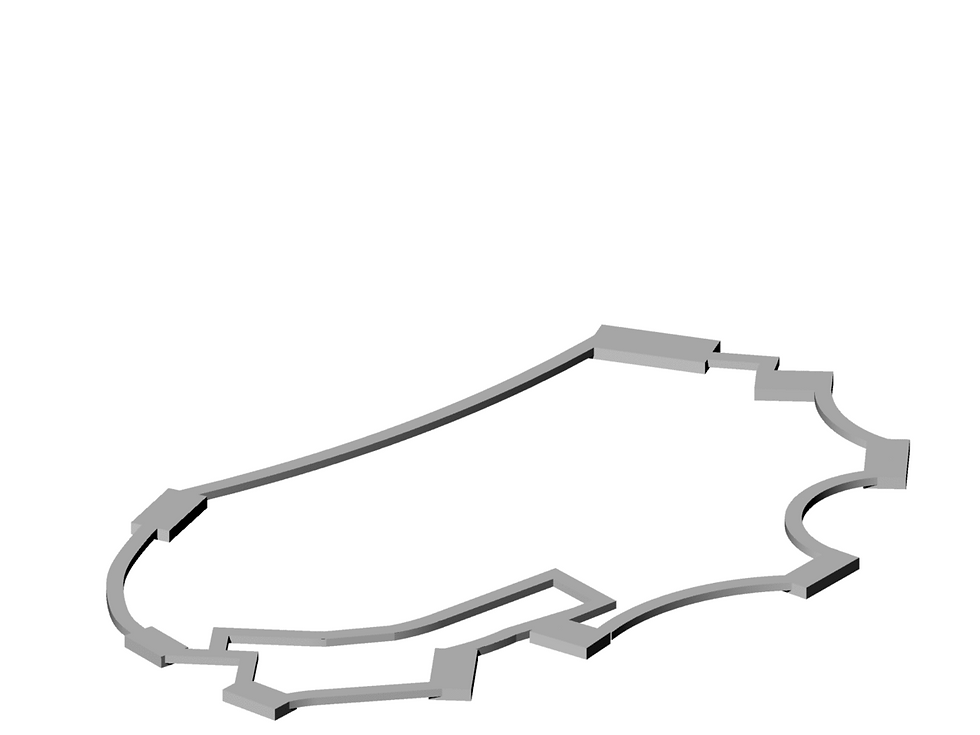
The design team developed two alternative approaches. The first was a simple, welded steel pipe-frame. This strategy was cost effective and low-tech while still maintaining a thin profile for the shell and structure assembly.
The second option employed a steel tube superstructure to carry a panelized, unitized assembly. With Zahner joining the team as the shell fabricator, we were able to apply their breadth of expertise in digital fabrication and complex geometric facades to determine this strategy as the preferred option.
Bringing Zahner into the design process enabled us to leverage their existing proprietary systems such as their “D” extrusion and “Zepps” panels. But these details, while incredibly adaptive, were unsightly because they had originally been designed to be hidden within building facades. In their application on the Chrysalis, both front and back of unitized panels would be exposed in plain view. The team worked together to rework the system to be more elegant, orderly and visually appealing.
On-site construction was rapid because the superstructure and shell designs were systematized. The process was fully coordinated with sections arriving pre-assembled and coded for easy erection.
Project done at Living Design Lab. Click button below for list of entire design team.

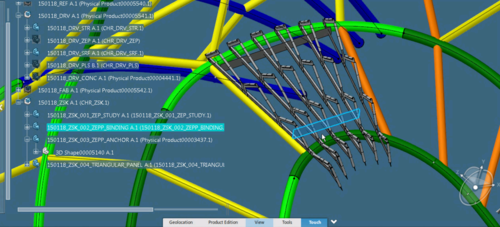

.jpg)
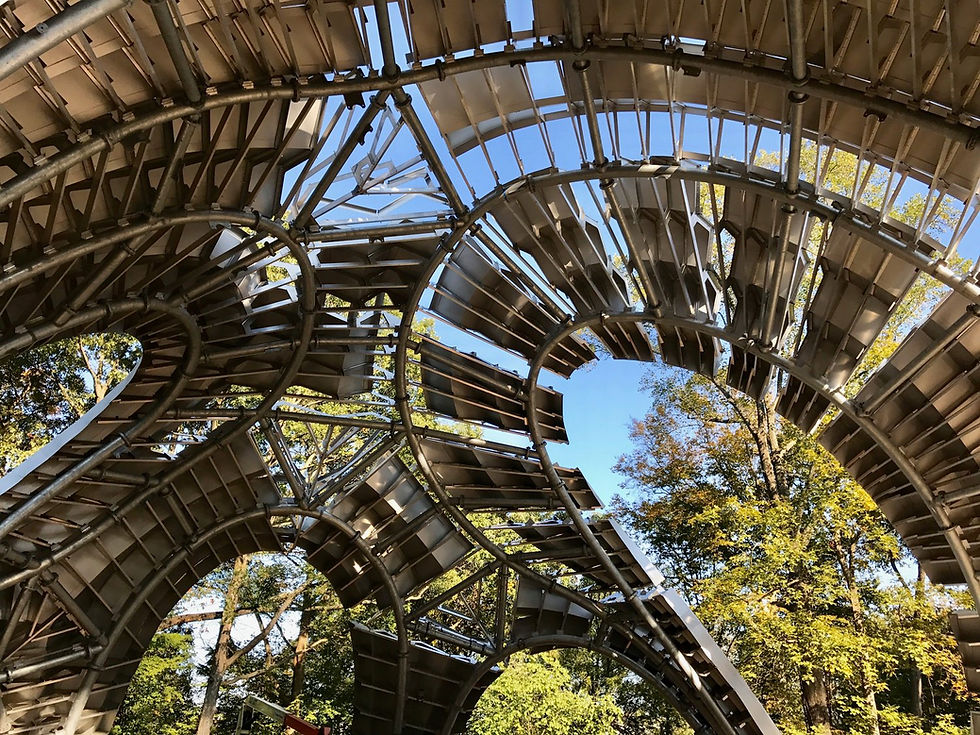.jpg)
